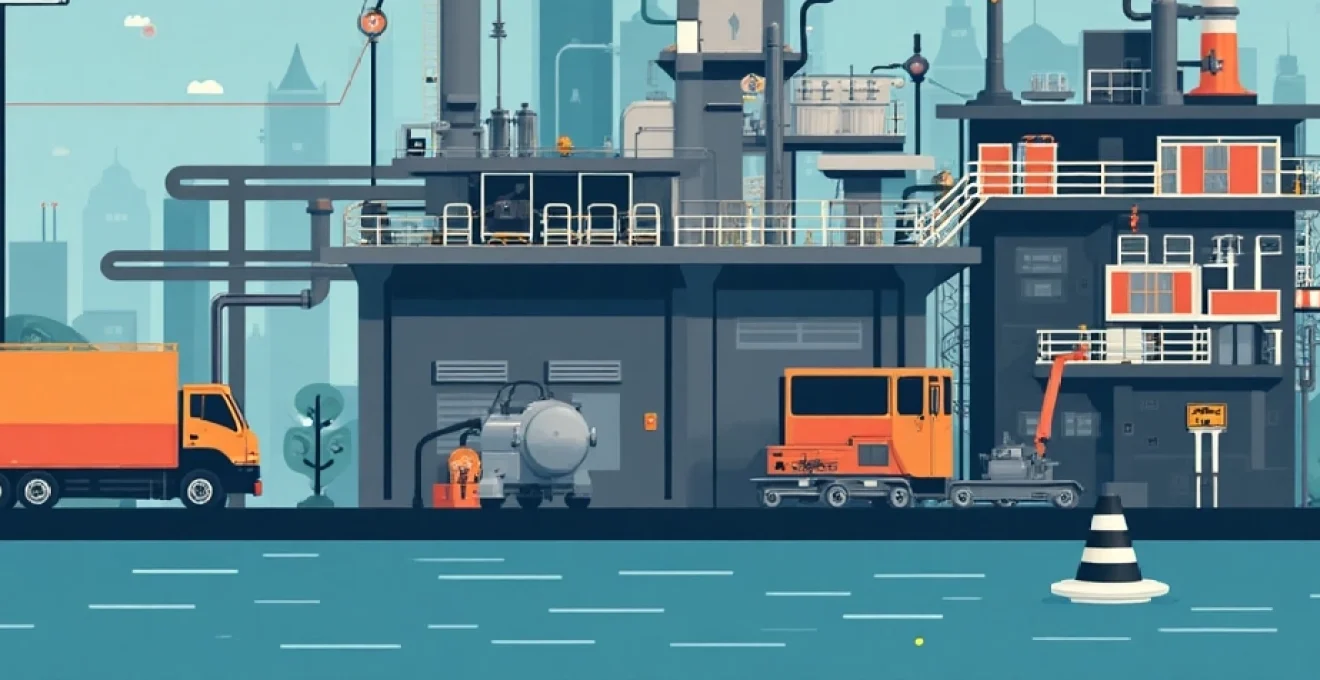
Les dommages causés par des éléments d’équipement défectueux représentent un enjeu majeur pour les industries et les entreprises. Ces défaillances peuvent entraîner des conséquences graves, allant de simples perturbations opérationnelles à des accidents catastrophiques. Comprendre les mécanismes de ces défaillances, leurs causes profondes et les moyens de les prévenir est essentiel pour garantir la sécurité, la fiabilité et la performance des installations industrielles. Dans un contexte où la complexité des systèmes ne cesse de croître, il est crucial d’adopter une approche proactive et globale pour gérer les risques liés aux équipements défectueux.
Types d’équipements défectueux et risques associés
Les équipements défectueux peuvent se manifester sous diverses formes, chacune présentant des risques spécifiques pour les opérations et la sécurité. Il est important de comprendre ces différentes catégories pour mieux appréhender les enjeux et mettre en place des stratégies de prévention adaptées.
Défaillances des systèmes hydrauliques et pneumatiques
Les systèmes hydrauliques et pneumatiques sont omniprésents dans l’industrie, de la machinerie lourde aux installations de production. Leurs défaillances peuvent avoir des conséquences particulièrement graves. Les fuites de fluide sous pression, par exemple, peuvent causer des blessures graves au personnel ou endommager d’autres équipements. Un dysfonctionnement des valves ou des actionneurs peut entraîner des mouvements incontrôlés des machines, mettant en danger les opérateurs et compromettant la qualité de la production.
Les causes de ces défaillances sont multiples : usure des joints, contamination du fluide, ou encore surcharge du système. La maintenance préventive joue un rôle crucial dans la prévention de ces problèmes. Des inspections régulières, le remplacement des composants usés et l’analyse de la qualité du fluide sont autant de mesures essentielles pour maintenir l’intégrité de ces systèmes critiques.
Dysfonctionnements des composants électriques et électroniques
Dans notre ère numérique, les composants électriques et électroniques sont au cœur de pratiquement tous les équipements industriels. Leur défaillance peut avoir des répercussions considérables sur l’ensemble d’un système. Les courts-circuits, les surtensions ou les défauts d’isolation peuvent non seulement endommager l’équipement lui-même, mais aussi provoquer des incendies ou des chocs électriques, mettant en danger la vie des travailleurs.
Les dysfonctionnements des systèmes de contrôle électronique peuvent entraîner des erreurs de production coûteuses ou des arrêts non planifiés. Dans certains cas, ces défaillances peuvent même compromettre la sécurité des processus critiques. Par exemple, un capteur défectueux dans une usine chimique pourrait conduire à une réaction incontrôlée avec des conséquences potentiellement catastrophiques.
Détérioration des structures mécaniques et matériaux
La détérioration des structures mécaniques et des matériaux constitue un autre aspect crucial des dommages causés par des équipements défectueux. La corrosion, la fatigue des matériaux et l’usure mécanique peuvent affaiblir progressivement les structures, conduisant à des ruptures soudaines et potentiellement catastrophiques. Ces problèmes sont particulièrement préoccupants dans les industries où les équipements sont soumis à des contraintes élevées ou à des environnements agressifs.
La détérioration peut se manifester de diverses manières : fissures dans les soudures, déformation des pièces métalliques, ou encore dégradation des revêtements protecteurs. Dans certains cas, ces défauts peuvent rester invisibles pendant longtemps, rendant leur détection d’autant plus cruciale. L’utilisation de techniques d’inspection avancées, telles que les ultrasons ou la thermographie, est souvent nécessaire pour identifier ces problèmes avant qu’ils ne deviennent critiques.
La prévention des dommages causés par la détérioration des matériaux nécessite une approche multidisciplinaire, combinant une conception robuste, une sélection judicieuse des matériaux et un programme de maintenance rigoureux.
Analyse des causes racines des défaillances d’équipement
L’analyse des causes racines est une étape fondamentale pour comprendre et prévenir les défaillances d’équipement. Cette approche systématique vise à identifier les facteurs sous-jacents qui contribuent aux défaillances, plutôt que de se concentrer uniquement sur les symptômes immédiats. En comprenant ces causes profondes, vous pouvez développer des stratégies de prévention plus efficaces et durables.
Fatigue des matériaux et vieillissement prématuré
La fatigue des matériaux est un phénomène insidieux qui peut affecter pratiquement tous les types d’équipements mécaniques. Elle se produit lorsqu’un matériau est soumis à des charges répétées, même si ces charges sont bien en deçà de sa limite d’élasticité. Au fil du temps, de minuscules fissures peuvent se former et se propager, conduisant éventuellement à une rupture catastrophique.
Le vieillissement prématuré des équipements peut être causé par divers facteurs environnementaux tels que la chaleur excessive, l’humidité, les vibrations ou l’exposition à des produits chimiques agressifs. Ces conditions peuvent accélérer la dégradation des matériaux, réduisant considérablement la durée de vie prévue des équipements. Il est crucial de prendre en compte ces facteurs lors de la conception et de l’installation des équipements pour minimiser leur impact à long terme.
Erreurs de conception et dimensionnement inadéquat
Les erreurs de conception et le dimensionnement inadéquat sont souvent à l’origine de défaillances d’équipement récurrentes. Ces problèmes peuvent résulter d’une mauvaise compréhension des conditions d’utilisation réelles, d’une sous-estimation des charges ou d’une négligence des facteurs de sécurité appropriés. Par exemple, un système de refroidissement sous-dimensionné peut entraîner une surchauffe chronique, accélérant l’usure des composants et augmentant le risque de panne.
Les erreurs de conception peuvent également se manifester dans le choix inapproprié des matériaux ou dans l’agencement des composants. Une interface mal conçue entre deux pièces peut créer des points de concentration de contraintes, augmentant le risque de rupture par fatigue. Il est essentiel d’impliquer des experts en ingénierie dès les premières phases de conception pour éviter ces pièges coûteux.
Maintenance préventive insuffisante ou inadaptée
Une maintenance préventive insuffisante ou mal adaptée est une cause fréquente de défaillances d’équipement. Trop souvent, les entreprises adoptent une approche réactive, n’intervenant que lorsqu’un problème se manifeste. Cette stratégie peut sembler économiser des ressources à court terme, mais elle conduit généralement à des pannes plus fréquentes et plus coûteuses sur le long terme.
Une maintenance préventive efficace nécessite une planification minutieuse et une exécution rigoureuse. Elle doit être basée sur une compréhension approfondie des modes de défaillance potentiels de chaque équipement et adaptée aux conditions spécifiques d’utilisation. L’utilisation de technologies de surveillance avancées, comme l’analyse des vibrations ou la thermographie infrarouge, peut grandement améliorer l’efficacité des programmes de maintenance préventive.
Conditions d’utilisation hors spécifications
L’utilisation d’équipements dans des conditions qui dépassent leurs spécifications de conception est une cause majeure de défaillances prématurées. Cela peut inclure des facteurs tels que des charges excessives, des températures extrêmes, ou une exposition à des substances corrosives non prévues. Parfois, ces conditions résultent d’une évolution des processus de production sans une réévaluation adéquate de la capacité des équipements existants.
Il est crucial de maintenir une documentation précise des spécifications de chaque équipement et de former régulièrement le personnel opérationnel sur les limites d’utilisation. De plus, tout changement dans les conditions d’exploitation doit déclencher une évaluation des impacts potentiels sur les équipements. L’installation de systèmes de surveillance en temps réel peut aider à détecter rapidement les déviations par rapport aux conditions normales d’utilisation.
Méthodes d’évaluation et de prévention des dommages
La prévention efficace des dommages causés par des équipements défectueux repose sur une combinaison de méthodes d’évaluation avancées et de stratégies de prévention proactives. Ces approches permettent non seulement de détecter les problèmes potentiels avant qu’ils ne deviennent critiques, mais aussi d’optimiser la performance et la durée de vie des équipements.
Techniques d’inspection non destructive (CND)
Les techniques d’inspection non destructive (CND) jouent un rôle crucial dans l’évaluation de l’intégrité des équipements sans compromettre leur fonctionnalité. Ces méthodes permettent de détecter des défauts invisibles à l’œil nu, tels que des fissures internes, des zones de corrosion ou des défauts de soudure. Parmi les techniques les plus couramment utilisées, on trouve :
- Les ultrasons, pour détecter des fissures ou mesurer l’épaisseur des matériaux
- La radiographie, pour visualiser l’intérieur des structures
- Les courants de Foucault, particulièrement efficaces pour les matériaux conducteurs
- La thermographie infrarouge, pour identifier les zones de surchauffe ou d’isolation défectueuse
L’utilisation combinée de ces techniques permet d’obtenir une image complète de l’état des équipements. Par exemple, l’inspection par ultrasons d’une cuve sous pression peut révéler des zones d’amincissement dues à la corrosion, permettant une intervention préventive avant qu’une rupture ne se produise.
Analyse des modes de défaillance (AMDEC)
L’Analyse des Modes de Défaillance, de leurs Effets et de leur Criticité (AMDEC) est une méthode systématique pour identifier et prévenir les problèmes potentiels dans un système ou un processus avant qu’ils ne surviennent. Cette approche proactive implique :
- L’identification de tous les modes de défaillance possibles
- L’évaluation de leurs effets potentiels
- La détermination de leur probabilité d’occurrence et de leur gravité
- La mise en place de mesures préventives pour les modes de défaillance les plus critiques
L’AMDEC est particulièrement efficace lorsqu’elle est réalisée dès la phase de conception d’un équipement. Elle permet d’anticiper les problèmes potentiels et d’intégrer des solutions préventives avant même que l’équipement ne soit mis en service. Cette méthode peut également être appliquée aux équipements existants pour améliorer leur fiabilité et leur sécurité.
Systèmes de surveillance en temps réel
Les systèmes de surveillance en temps réel représentent une avancée majeure dans la prévention des dommages causés par des équipements défectueux. Ces systèmes utilisent des capteurs sophistiqués pour collecter en continu des données sur les paramètres critiques des équipements, tels que la température, les vibrations, la pression ou la consommation électrique. Ces données sont analysées en temps réel pour détecter toute anomalie ou tendance préoccupante.
L’un des avantages clés de ces systèmes est leur capacité à détecter des problèmes naissants bien avant qu’ils ne deviennent visibles ou critiques. Par exemple, une augmentation progressive des vibrations d’une machine tournante peut indiquer un déséquilibre ou une usure des roulements, permettant une intervention préventive avant une défaillance catastrophique.
Les systèmes de surveillance en temps réel, couplés à l’intelligence artificielle, ouvrent la voie à une maintenance prédictive de plus en plus précise et efficace.
Programmes de maintenance prédictive
La maintenance prédictive représente l’évolution naturelle des approches traditionnelles de maintenance préventive. Plutôt que de se baser sur des intervalles fixes, la maintenance prédictive utilise des données en temps réel et des analyses avancées pour prédire quand un équipement nécessitera une intervention. Cette approche permet d’optimiser les interventions de maintenance, réduisant ainsi les temps d’arrêt inutiles tout en prévenant les pannes inattendues.
Un programme de maintenance prédictive efficace combine généralement plusieurs technologies :
- Analyse des vibrations pour détecter les problèmes mécaniques
- Analyse des huiles pour évaluer l’état des systèmes lubrifiés
- Thermographie pour identifier les points chauds anormaux
- Analyse acoustique pour détecter les fuites ou les défauts de fonctionnement
Ces données sont ensuite analysées à l’aide d’algorithmes sophistiqués pour prédire quand et où une défaillance est susceptible de se produire. Cette approche permet non seulement de prévenir les pannes, mais aussi d’optimiser la durée de vie des équipements et de réduire les coûts de maintenance globaux.
Cadre juridique et normatif
Le cadre juridique et normatif entourant les dommages causés par des équipements défectueux est complexe et en constante évolution. Il vise à établir des standards de sécurité, à définir les responsabilités des différents acteurs et à encadrer les procédures de gestion des risques. Comprendre ce cadre est essentiel pour toute entreprise souhaitant gérer efficacement ses risques liés aux équipements.
Responsabilité du fait des produits défectueux
La responsabilité du fait des produits défectueux est un concept juridique crucial dans le contexte des dommages causés par des équipements. Elle impose une respons
abilité accrue sur les fabricants et les distributeurs d’équipements. En Europe, la directive 85/374/CEE, transposée dans les législations nationales, établit le principe de la responsabilité sans faute du producteur. Cela signifie que le fabricant peut être tenu responsable des dommages causés par un produit défectueux, même en l’absence de négligence prouvée.
Cette responsabilité s’étend non seulement aux dommages corporels, mais aussi aux dommages matériels. Par exemple, si un compresseur industriel défectueux cause une explosion dans une usine, le fabricant pourrait être tenu responsable non seulement des blessures éventuelles, mais aussi des dégâts matériels causés à l’installation.
Il est important de noter que cette responsabilité n’est pas absolue. Le producteur peut s’exonérer dans certains cas, notamment s’il prouve que l’état des connaissances scientifiques et techniques au moment de la mise en circulation du produit ne permettait pas de déceler l’existence du défaut. Cette « exception du risque de développement » souligne l’importance pour les fabricants de rester à la pointe de la recherche et du développement dans leur domaine.
Normes ISO et directives européennes applicables
Les normes ISO et les directives européennes jouent un rôle crucial dans l’établissement de standards de sécurité et de qualité pour les équipements industriels. Ces normes fournissent un cadre de référence pour la conception, la fabrication et l’utilisation des équipements, visant à minimiser les risques de défaillance et leurs conséquences.
Parmi les normes ISO pertinentes, on peut citer :
- ISO 9001 pour les systèmes de management de la qualité
- ISO 14001 pour le management environnemental
- ISO 45001 pour la santé et la sécurité au travail
Ces normes, bien que volontaires, sont souvent exigées par les clients et peuvent constituer un avantage concurrentiel significatif. Elles imposent une approche systématique de la gestion des risques et de l’amélioration continue, ce qui contribue à réduire les risques de défaillance des équipements.
Au niveau européen, plusieurs directives encadrent la sécurité des équipements, notamment :
- La directive Machines 2006/42/CE
- La directive Équipements sous pression 2014/68/UE
- La directive Basse tension 2014/35/UE
Ces directives établissent des exigences essentielles de sécurité que les équipements doivent respecter pour pouvoir être mis sur le marché européen. Elles imposent également des procédures d’évaluation de la conformité, qui peuvent inclure des tests par des organismes notifiés indépendants.
Procédures de rappel et actions correctives
Lorsqu’un défaut est identifié sur un équipement déjà en circulation, les fabricants et les distributeurs ont l’obligation légale et morale de prendre des mesures correctives. Ces actions peuvent aller de simples avertissements aux utilisateurs jusqu’au rappel complet des produits concernés.
Les procédures de rappel sont particulièrement cruciales pour limiter les dommages potentiels. Elles doivent être rapides, efficaces et transparentes. Un rappel bien géré peut non seulement prévenir des accidents, mais aussi renforcer la confiance des consommateurs dans la marque. À l’inverse, un rappel mal géré peut avoir des conséquences désastreuses en termes d’image et de responsabilité légale.
Une communication claire et proactive est essentielle lors d’un rappel de produit. Elle démontre la responsabilité de l’entreprise et son engagement envers la sécurité de ses clients.
Les actions correctives ne se limitent pas au simple rappel des produits. Elles peuvent inclure :
- Des modifications de conception pour éliminer le défaut
- Des mises à jour des manuels d’utilisation et des formations pour les utilisateurs
- Des inspections et des réparations sur site des équipements installés
- Des améliorations des processus de contrôle qualité pour prévenir la récurrence du problème
Il est crucial que ces actions soient documentées de manière exhaustive. Cette documentation peut être essentielle en cas de litige ultérieur pour démontrer la diligence de l’entreprise dans la gestion du problème.
Stratégies de gestion des risques et assurance
Face aux risques liés aux équipements défectueux, les entreprises doivent adopter une approche globale de gestion des risques. Cette stratégie doit combiner des mesures préventives, des couvertures d’assurance adaptées et des plans de réponse en cas d’incident.
Polices d’assurance spécifiques aux défaillances d’équipement
Les polices d’assurance spécifiques aux défaillances d’équipement sont un élément crucial de la stratégie de gestion des risques d’une entreprise. Ces polices, souvent appelées « assurance bris de machine » ou « assurance tous risques chantier », offrent une protection financière contre les pertes directes et indirectes résultant de la défaillance d’équipements critiques.
Les principales caractéristiques de ces polices incluent généralement :
- La couverture des dommages matériels à l’équipement lui-même
- L’indemnisation des pertes d’exploitation résultant de la panne
- La prise en charge des frais de réparation ou de remplacement
- Dans certains cas, la couverture des dommages causés à d’autres biens ou à des tiers
Il est crucial de choisir une police adaptée aux risques spécifiques de l’entreprise. Par exemple, une usine chimique aura besoin d’une couverture différente de celle d’un centre de données. La police doit être régulièrement révisée pour s’assurer qu’elle reste adéquate face à l’évolution des équipements et des risques.
Plans de continuité d’activité et gestion de crise
Un plan de continuité d’activité (PCA) est essentiel pour minimiser l’impact d’une défaillance d’équipement sur les opérations de l’entreprise. Ce plan doit identifier les processus critiques, les équipements clés et les ressources nécessaires pour maintenir ou reprendre rapidement les activités essentielles en cas d’incident.
Les éléments clés d’un PCA efficace incluent :
- L’analyse d’impact sur l’activité pour identifier les processus critiques
- L’identification des équipements de secours ou des alternatives opérationnelles
- Des procédures détaillées pour la reprise des activités
- Un plan de communication clair pour informer toutes les parties prenantes
- Des tests réguliers pour s’assurer de l’efficacité du plan
En parallèle, un plan de gestion de crise doit être élaboré pour gérer les aspects plus larges d’un incident majeur, y compris la communication avec les médias, les autorités et les clients. Ce plan doit définir clairement les rôles et responsabilités, les procédures de prise de décision et les canaux de communication à utiliser en situation de crise.
Formation du personnel à la sécurité des équipements
La formation du personnel est un élément crucial dans la prévention des dommages causés par des équipements défectueux. Un personnel bien formé peut non seulement prévenir de nombreux incidents, mais aussi réagir efficacement lorsqu’un problème survient.
Un programme de formation complet devrait couvrir :
- Les procédures d’utilisation sûre des équipements
- La reconnaissance des signes avant-coureurs de défaillance
- Les procédures d’urgence en cas de dysfonctionnement
- Les techniques de maintenance préventive de base
- La compréhension des risques spécifiques liés à chaque type d’équipement
La formation ne doit pas être un événement ponctuel, mais un processus continu. Des mises à jour régulières, des exercices pratiques et des simulations d’incidents peuvent aider à maintenir un haut niveau de vigilance et de compétence parmi le personnel.
Investir dans la formation du personnel est investir dans la sécurité et la fiabilité de l’ensemble de l’organisation. Un employé bien formé est la première ligne de défense contre les défaillances d’équipement.
En conclusion, la gestion efficace des risques liés aux équipements défectueux nécessite une approche multidimensionnelle. Elle combine des aspects techniques, organisationnels et humains. En mettant en place des stratégies robustes de prévention, de détection précoce et de réponse rapide, les entreprises peuvent considérablement réduire les risques de dommages graves et assurer la continuité de leurs opérations face aux défis posés par les défaillances d’équipement.