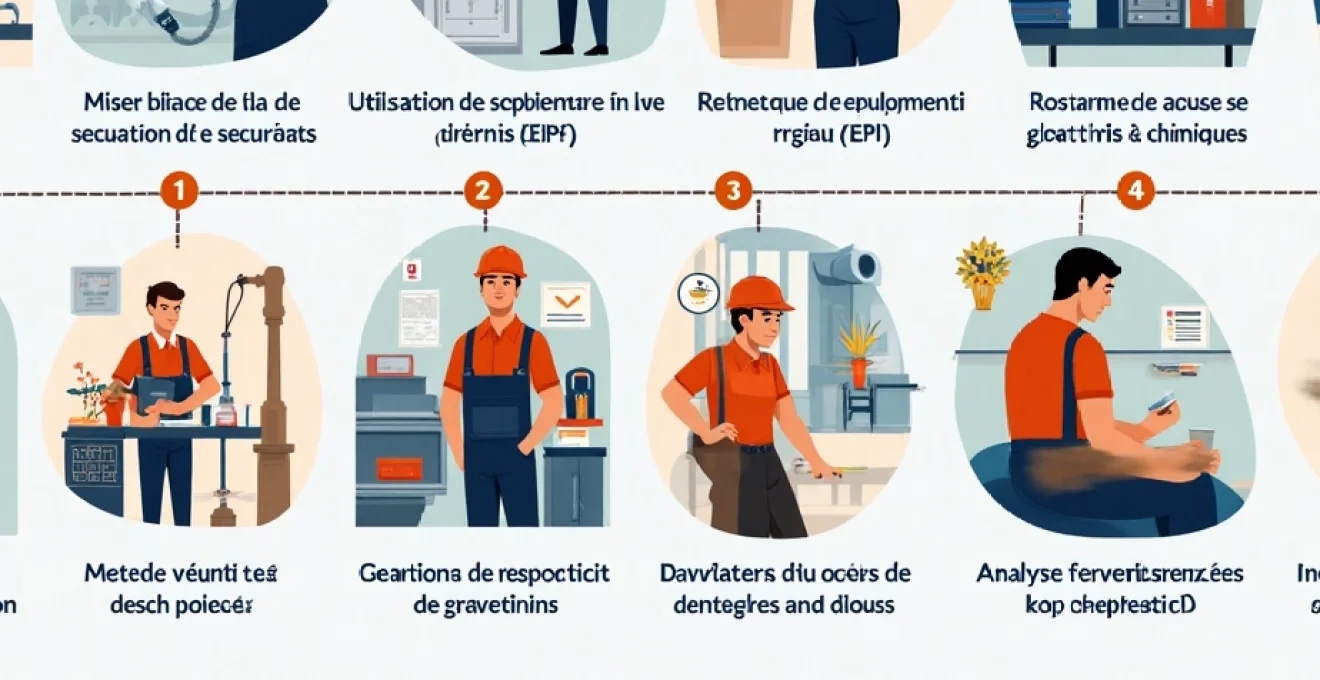
Les interventions de dépannage sont cruciales pour maintenir la continuité des opérations dans de nombreux secteurs. Qu’il s’agisse d’une panne électrique, d’un dysfonctionnement mécanique ou d’une urgence industrielle, la rapidité et l’efficacité de l’intervention sont primordiales. Une approche structurée et méthodique permet non seulement de résoudre le problème immédiat, mais aussi d’éviter sa récurrence. Cette méthodologie rigoureuse, associée à des compétences techniques pointues, constitue le socle d’une intervention de dépannage réussie.
Diagnostic initial et évaluation de la situation d’urgence
La première étape d’une intervention de dépannage efficace consiste à réaliser un diagnostic initial précis et une évaluation approfondie de la situation d’urgence. Cette phase est cruciale car elle détermine l’orientation de toute l’intervention. Le technicien doit rapidement analyser les symptômes, identifier les systèmes affectés et évaluer l’ampleur du problème.
Pour effectuer ce diagnostic, il est essentiel de procéder de manière systématique. Commencez par recueillir toutes les informations disponibles auprès des opérateurs ou des utilisateurs présents sur le site. Leurs observations peuvent fournir des indices précieux sur l’origine du problème. Ensuite, procédez à une inspection visuelle minutieuse de l’équipement ou de l’installation concernée.
Utilisez vos sens pour détecter des signes anormaux : bruits inhabituels, odeurs suspectes, températures anormales ou vibrations excessives. Ces indices peuvent souvent guider vers la source du problème. N’hésitez pas à utiliser des outils de diagnostic spécialisés comme des multimètres, des caméras thermiques ou des analyseurs de vibrations pour obtenir des données plus précises.
Une fois les informations collectées, il est important de les analyser rapidement pour formuler des hypothèses sur la cause probable de la panne. Cette analyse doit prendre en compte non seulement les symptômes actuels, mais aussi l’historique de maintenance de l’équipement et les conditions d’exploitation récentes. Une compréhension globale de la situation permet de prioriser les actions à entreprendre et d’optimiser le temps d’intervention.
Sécurisation de la zone d’intervention
Après le diagnostic initial, la sécurisation de la zone d’intervention devient une priorité absolue. Cette étape est fondamentale pour garantir la sécurité du personnel intervenant, des utilisateurs de l’équipement et de l’environnement immédiat. Une zone d’intervention sécurisée permet également de travailler plus efficacement, sans risque d’aggravation du problème ou de création de nouveaux dangers.
Mise en place du périmètre de sécurité
La mise en place d’un périmètre de sécurité est la première action à entreprendre pour sécuriser la zone d’intervention. Ce périmètre doit être clairement délimité et suffisamment large pour englober non seulement l’équipement défectueux, mais aussi l’espace nécessaire aux manœuvres des intervenants. Utilisez des barrières physiques, des rubans de signalisation ou des cônes de sécurité pour marquer clairement les limites de la zone d’intervention.
Assurez-vous que tous les accès à la zone sont contrôlés et que seul le personnel autorisé peut y pénétrer. Installez une signalétique appropriée pour informer sur la nature de l’intervention en cours et les risques potentiels. Cette communication visuelle est essentielle pour prévenir les accidents et sensibiliser toutes les personnes présentes sur le site.
Utilisation d’équipements de protection individuelle (EPI)
L’utilisation adéquate des équipements de protection individuelle (EPI) est cruciale pour la sécurité des intervenants. Les EPI doivent être adaptés à la nature de l’intervention et aux risques spécifiques identifiés lors du diagnostic initial. Cela peut inclure des casques de sécurité, des lunettes de protection, des gants isolants, des chaussures de sécurité, ou encore des protections auditives.
Il est important de vérifier l’état et la conformité des EPI avant chaque utilisation. Un équipement endommagé ou inadapté peut créer un faux sentiment de sécurité et exposer le technicien à des risques accrus. Formez régulièrement votre équipe à l’utilisation correcte des EPI et insistez sur l’importance de les porter systématiquement, même pour des interventions de courte durée.
Gestion des risques électriques et chimiques
La gestion des risques électriques et chimiques requiert une attention particulière lors des interventions de dépannage. Pour les risques électriques, commencez par couper l’alimentation de l’équipement concerné et vérifiez l’absence de tension à l’aide d’un voltmètre certifié. Utilisez des outils isolés et respectez scrupuleusement les procédures de consignation/déconsignation.
Concernant les risques chimiques, identifiez tous les produits potentiellement dangereux présents dans la zone d’intervention. Consultez les fiches de données de sécurité (FDS) pour connaître les précautions à prendre et les EPI spécifiques à utiliser. Assurez-vous que des kits de décontamination et des douches de sécurité sont disponibles à proximité en cas d’exposition accidentelle.
La sécurité n’est pas une option, c’est une condition sine qua non de toute intervention de dépannage réussie.
Techniques de dépannage rapide
Une fois la zone sécurisée, il est temps de mettre en œuvre des techniques de dépannage rapide pour résoudre le problème identifié. Ces techniques doivent allier efficacité et précision pour minimiser le temps d’arrêt de l’équipement tout en assurant une résolution durable du problème.
Méthode SWOT appliquée au dépannage
La méthode SWOT, traditionnellement utilisée en stratégie d’entreprise, peut être adaptée avec succès aux interventions de dépannage. Dans ce contexte, SWOT signifie : Symptômes, Wiring (câblage), Output (résultats), et Tests. Cette approche structurée permet d’aborder le problème de manière systématique :
- Symptômes : Analysez en détail les manifestations du problème.
- Wiring : Vérifiez tous les aspects du câblage et des connexions.
- Output : Mesurez et comparez les résultats obtenus avec les valeurs attendues.
- Tests : Effectuez des tests ciblés pour confirmer ou infirmer vos hypothèses.
Cette méthode permet de structurer la réflexion et d’éviter les oublis lors de l’analyse du problème. Elle favorise une approche méthodique qui augmente les chances de trouver rapidement la cause racine du dysfonctionnement.
Utilisation d’outils de diagnostic avancés
Les outils de diagnostic avancés jouent un rôle crucial dans l’accélération et la précision des interventions de dépannage. Parmi ces outils, on trouve des analyseurs de réseau , des oscilloscopes portables , des caméras thermiques et des systèmes de surveillance vibratoire . Ces équipements permettent de collecter des données précises sur le fonctionnement de l’installation et de détecter des anomalies invisibles à l’œil nu.
Par exemple, une caméra thermique peut rapidement identifier des points chauds dans un tableau électrique, révélant des connexions desserrées ou des composants surchargés. Un analyseur de vibrations peut détecter des problèmes mécaniques naissants dans des machines tournantes, permettant une intervention précoce avant une panne catastrophique.
L’utilisation efficace de ces outils requiert une formation adéquate et une expérience pratique. Investir dans la formation continue de vos techniciens sur ces technologies de pointe peut significativement améliorer la qualité et la rapidité de vos interventions de dépannage.
Réparations temporaires vs solutions permanentes
Dans le contexte d’une intervention de dépannage, il est parfois nécessaire de faire un choix entre une réparation temporaire et une solution permanente. Ce choix dépend de plusieurs facteurs, notamment l’urgence de la situation, la disponibilité des pièces de rechange et l’impact sur la production.
Une réparation temporaire peut être envisagée lorsque l’arrêt prolongé de l’équipement aurait des conséquences graves sur l’activité. Cependant, il est crucial de bien documenter cette intervention provisoire et de planifier une intervention ultérieure pour une réparation définitive. Assurez-vous que la réparation temporaire ne compromet pas la sécurité et n’entraîne pas de dommages supplémentaires à l’équipement.
Pour les solutions permanentes, privilégiez des approches qui non seulement résolvent le problème immédiat mais améliorent également la fiabilité globale de l’installation. Cela peut impliquer le remplacement de composants par des versions plus robustes, la mise à niveau de systèmes obsolètes ou l’ajout de dispositifs de surveillance pour prévenir les pannes futures.
La décision entre une réparation temporaire et une solution permanente doit toujours être prise en considérant l’équilibre entre les besoins opérationnels immédiats et la fiabilité à long terme de l’installation.
Communication et coordination avec les parties prenantes
La communication et la coordination efficaces avec toutes les parties prenantes sont des aspects souvent sous-estimés mais cruciaux d’une intervention de dépannage réussie. Une bonne communication permet non seulement de faciliter l’intervention elle-même, mais aussi de gérer les attentes et de maintenir la confiance des clients ou des utilisateurs impactés par la panne.
Dès le début de l’intervention, établissez une ligne de communication claire avec le client ou le responsable du site. Informez-les régulièrement de l’avancement du diagnostic, des actions entreprises et du temps estimé pour la résolution du problème. Cette transparence aide à réduire l’anxiété et permet aux parties prenantes de prendre des décisions éclairées concernant leurs propres opérations.
Coordonnez-vous efficacement avec les autres services ou équipes impliqués dans l’intervention. Cela peut inclure le service de sécurité pour la gestion des accès, le service de production pour la planification des arrêts, ou encore le service logistique pour l’approvisionnement en pièces de rechange. Une coordination fluide évite les retards inutiles et optimise l’efficacité de l’intervention.
N’oubliez pas d’impliquer les opérateurs ou les utilisateurs habituels de l’équipement dans le processus de dépannage. Leur connaissance intime du fonctionnement quotidien peut fournir des indices précieux pour identifier la cause du problème. De plus, leur implication favorise l’adhésion aux solutions proposées et facilite la mise en œuvre de nouvelles procédures si nécessaire.
Utilisez des outils de communication adaptés à la situation. Dans certains cas, un simple groupe de messagerie instantanée peut suffire pour tenir toutes les parties informées en temps réel. Pour des interventions plus complexes, envisagez l’utilisation de plateformes de gestion de projet collaboratives qui permettent de centraliser les informations, de suivre l’avancement et de partager des documents importants.
Documentation et suivi post-intervention
La phase de documentation et de suivi post-intervention est cruciale pour capitaliser sur l’expérience acquise et améliorer continuellement les processus de maintenance. Une documentation précise et complète permet non seulement de faciliter les futures interventions sur le même équipement, mais aussi d’alimenter une base de connaissances précieuse pour l’ensemble de l’équipe de maintenance.
Rédaction du rapport d’intervention
La rédaction d’un rapport d’intervention détaillé est une étape incontournable de toute intervention de dépannage. Ce document doit être rédigé avec soin et inclure tous les éléments pertinents de l’intervention. Voici les principaux éléments à inclure dans un rapport d’intervention complet :
- Informations de base : date, heure, lieu, équipement concerné, intervenants
- Description détaillée du problème initial
- Diagnostic posé et méthodes utilisées pour y parvenir
- Actions entreprises et solutions mises en œuvre
- Pièces remplacées ou réparées (avec références)
- Temps passé sur l’intervention
- Résultats des tests post-intervention
- Recommandations pour éviter la récurrence du problème
Utilisez un langage clair et précis, évitez le jargon excessif et incluez des photos ou des schémas si nécessaire pour illustrer certains aspects de l’intervention. Un rapport bien rédigé constitue un outil précieux pour le suivi de l’équipement et peut servir de référence pour des formations futures.
Analyse des causes racines (méthode des 5 pourquoi)
L’analyse des causes racines est une étape cruciale pour prévenir la récurrence des problèmes. La méthode des 5 Pourquoi est une technique simple mais efficace pour aller au-delà des symptômes apparents et identifier les causes fondamentales d’un problème. Elle consiste à poser la question « Pourquoi ? » de manière répétée, généralement cinq fois, pour creuser en profondeur les raisons d’un dysfonctionnement.
Par exemple, si une machine s’est arrêtée en raison d’une surchauffe, l’analyse pourrait se dérouler ainsi :
- Pourquoi la machine a-t-elle surchauffé ? Parce que le système de refroidissement ne fonctionnait pas correctement.
- Pourquoi le système de refroidissement ne fonctionnait-il pas correctement ? Parce que la pompe de circulation était défectueuse.
- Pourquoi la pompe était-elle défectueuse ? Parce que les paliers étaient usés.
- Pourquoi les paliers étaient-ils usés ? Parce qu’ils n
‘avaient pas été lubrifiés correctement.
Cette analyse révèle que la cause racine du problème n’était pas simplement une pompe défectueuse, mais une lacune dans le programme de maintenance préventive. Cette information est cruciale pour prévenir des problèmes similaires à l’avenir, non seulement sur cet équipement spécifique, mais potentiellement sur d’autres systèmes similaires dans l’installation.
Mise à jour des procédures de maintenance préventive
Suite à l’analyse des causes racines, il est essentiel de mettre à jour les procédures de maintenance préventive pour intégrer les leçons apprises lors de l’intervention de dépannage. Cette étape est cruciale pour prévenir la récurrence des problèmes et améliorer la fiabilité globale des équipements.
Commencez par revoir le plan de maintenance existant à la lumière des nouvelles informations. Identifiez les points faibles ou les omissions qui ont pu contribuer au problème. Dans notre exemple précédent, cela impliquerait d’ajouter des vérifications régulières de la lubrification des pompes au programme de maintenance.
Ensuite, élaborez de nouvelles procédures ou modifiez celles existantes pour combler les lacunes identifiées. Assurez-vous que ces procédures sont claires, détaillées et facilement compréhensibles par tous les techniciens. Incluez des points de contrôle spécifiques, des fréquences d’intervention recommandées et des critères précis pour évaluer l’état des équipements.
N’oubliez pas de former votre équipe de maintenance sur ces nouvelles procédures. Une formation adéquate garantit que les changements seront effectivement mis en œuvre et que tout le personnel comprend l’importance de ces mises à jour.
La mise à jour des procédures de maintenance préventive n’est pas une tâche ponctuelle, mais un processus continu d’amélioration basé sur l’expérience acquise lors de chaque intervention.
Enfin, mettez en place un système de suivi pour évaluer l’efficacité des nouvelles procédures. Cela peut inclure des indicateurs de performance clés (KPI) tels que le temps moyen entre les pannes (MTBF) ou le taux de pannes récurrentes. Analysez régulièrement ces données pour identifier d’autres opportunités d’amélioration et ajustez vos procédures en conséquence.
En suivant ce processus rigoureux de documentation, d’analyse et d’amélioration continue, vous transformez chaque intervention de dépannage en une opportunité d’apprentissage et d’optimisation pour votre organisation. Cette approche proactive de la maintenance non seulement réduit les temps d’arrêt et les coûts associés aux pannes, mais contribue également à prolonger la durée de vie des équipements et à améliorer la productivité globale de l’installation.