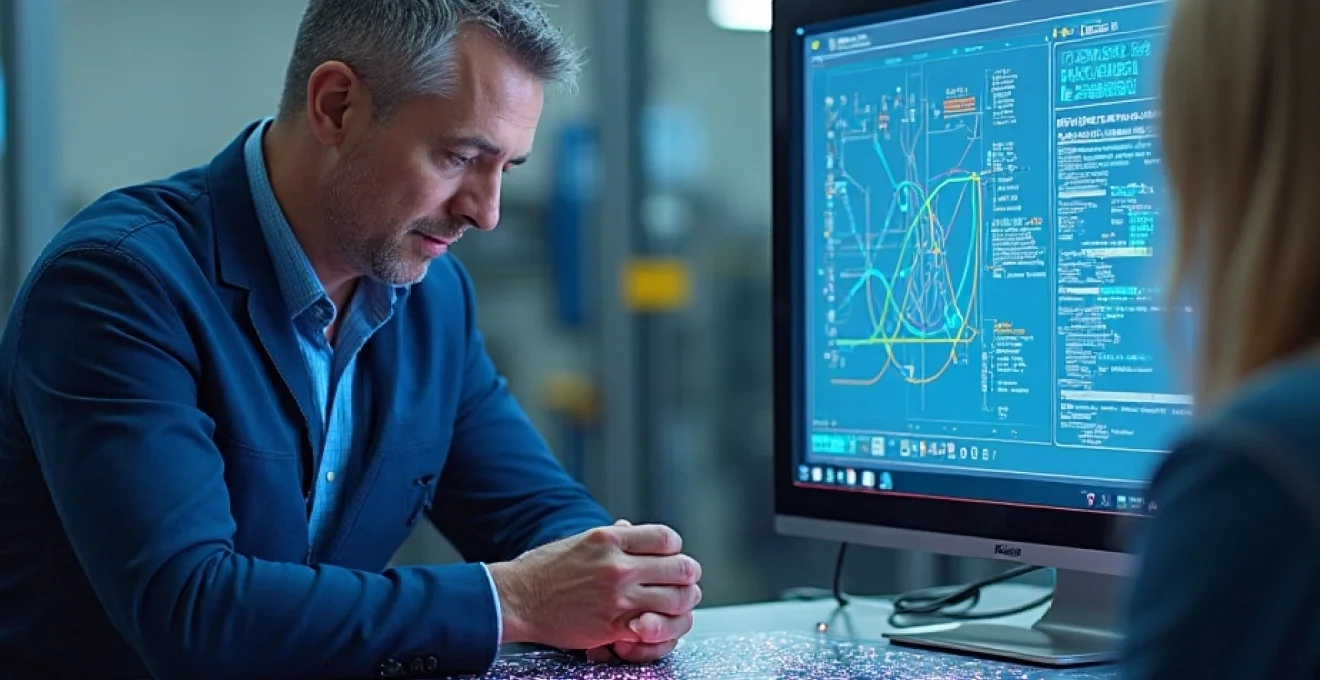
La remise en état rapide des équipements défaillants est un enjeu crucial pour maintenir la productivité et la rentabilité des installations industrielles. Que ce soit dans le secteur manufacturier, l’agroalimentaire ou l’énergie, chaque minute d’arrêt se traduit par des pertes financières significatives. Pour faire face à ce défi, les techniciens de maintenance doivent maîtriser un ensemble de compétences et de techniques permettant de diagnostiquer efficacement les pannes, d’effectuer les réparations nécessaires et de remettre les équipements en service dans les plus brefs délais. Cette approche proactive de la maintenance est essentielle pour optimiser la disponibilité des machines et réduire les coûts opérationnels à long terme.
Diagnostic rapide des équipements défaillants
Le diagnostic rapide est la première étape cruciale pour remettre en état un équipement défaillant. Il s’agit d’identifier précisément la cause du dysfonctionnement pour intervenir de manière ciblée et efficace. Pour y parvenir, les techniciens disposent de plusieurs méthodes et outils.
L’analyse des symptômes est le point de départ du diagnostic. Les techniciens doivent être à l’écoute des opérateurs qui connaissent bien le fonctionnement normal des machines et peuvent décrire les anomalies observées. Des bruits inhabituels, des vibrations excessives ou des variations de performance sont autant d’indices précieux pour orienter les recherches.
L’inspection visuelle permet ensuite de repérer d’éventuels dommages apparents comme des pièces cassées, des connexions desserrées ou des fuites. Cette étape ne doit pas être négligée car elle peut révéler rapidement certains problèmes évidents.
L’utilisation d’appareils de mesure est indispensable pour effectuer un diagnostic précis. Les multimètres permettent de vérifier les tensions, intensités et résistances des circuits électriques. Les oscilloscopes visualisent les signaux électroniques pour détecter des anomalies. Des caméras thermiques peuvent révéler des échauffements anormaux.
L’analyse des données de maintenance est également précieuse. L’historique des interventions et les relevés des capteurs intégrés aux machines peuvent mettre en évidence des tendances ou des défaillances récurrentes. Ces informations orientent efficacement le diagnostic.
Un bon diagnostic est la clé d’une réparation rapide et durable. Il permet d’intervenir de manière ciblée sans perte de temps.
Enfin, l’expérience et l’expertise des techniciens jouent un rôle central. Leur connaissance approfondie des équipements leur permet souvent d’identifier rapidement l’origine d’une panne à partir de quelques indices. Cette capacité s’acquiert avec la pratique et la formation continue.
Techniques de réparation pour différents types de pannes
Une fois le diagnostic établi, les techniciens doivent mettre en œuvre les techniques de réparation adaptées selon le type de panne identifié. Les équipements industriels modernes combinent souvent des systèmes mécaniques, électriques, électroniques et informatiques. Il est donc essentiel de maîtriser un large éventail de compétences pour intervenir efficacement.
Réparation de circuits électroniques endommagés
Les cartes électroniques sont au cœur de nombreux équipements industriels. Leur réparation nécessite des compétences spécifiques et une grande minutie. La première étape consiste à localiser précisément le composant défectueux à l’aide d’appareils de mesure comme les oscilloscopes ou les testeurs de composants.
Une fois le composant identifié, il faut procéder à son remplacement en utilisant des techniques de soudage adaptées. L’utilisation d’une station de dessoudage permet de retirer proprement le composant endommagé sans endommager le circuit imprimé. Le nouveau composant est ensuite soudé avec précision.
Dans certains cas, la réparation peut nécessiter de refaire des pistes du circuit imprimé qui auraient été endommagées. Des techniques comme l’utilisation de fil de pontage ou la reconstruction de pistes à l’aide de résine conductrice permettent de restaurer la continuité électrique.
Remplacement de composants mécaniques usés
Les pannes mécaniques sont fréquentes sur les équipements industriels soumis à des contraintes importantes. Le remplacement des pièces usées ou endommagées nécessite souvent un démontage partiel de la machine. Il est crucial de suivre scrupuleusement les procédures du constructeur pour éviter tout dommage lors du démontage et du remontage.
Le choix des pièces de rechange est primordial pour garantir la fiabilité de la réparation. L’utilisation de pièces d’origine ou de qualité équivalente est recommandée. Dans certains cas, des pièces sur mesure peuvent être fabriquées pour remplacer des composants obsolètes.
Lors du remontage, un soin particulier doit être apporté aux réglages et aux alignements. L’utilisation d’outils spécifiques comme des comparateurs ou des lasers d’alignement permet d’assurer la précision nécessaire au bon fonctionnement de l’équipement.
Recalibrage des systèmes de contrôle
Les systèmes de contrôle jouent un rôle crucial dans le fonctionnement des équipements industriels modernes. Leur recalibrage est souvent nécessaire après une intervention ou lorsque des dérives sont constatées. Cette opération requiert une grande précision et l’utilisation d’instruments de mesure étalonnés.
Le recalibrage peut concerner des capteurs (température, pression, débit, etc.), des actionneurs (vannes, moteurs) ou des boucles de régulation complètes. Il s’agit d’ajuster les paramètres pour que les mesures et les actions de contrôle correspondent exactement aux valeurs attendues.
Dans certains cas, le recalibrage nécessite l’utilisation de logiciels spécifiques fournis par le constructeur de l’équipement. Ces outils permettent d’accéder aux paramètres internes du système de contrôle et de les modifier avec précision.
Résolution des problèmes logiciels et mise à jour du firmware
Les équipements industriels modernes intègrent de plus en plus de composants logiciels. La résolution des problèmes dans ce domaine nécessite des compétences en informatique industrielle. Les techniciens doivent être capables d’analyser les journaux d’erreurs, de diagnostiquer les dysfonctionnements et d’appliquer les correctifs nécessaires.
La mise à jour du firmware est souvent une solution efficace pour corriger des bugs ou améliorer les performances d’un équipement. Cette opération doit être menée avec précaution car une erreur peut rendre l’équipement inutilisable. Il est essentiel de suivre scrupuleusement les procédures recommandées par le constructeur et de sauvegarder les données importantes avant toute mise à jour.
Dans certains cas, la résolution des problèmes logiciels peut nécessiter une reprogrammation partielle de l’équipement. Les techniciens doivent alors maîtriser les langages de programmation spécifiques utilisés dans l’industrie comme le ladder
ou le structured text
.
Outils et équipements essentiels pour la remise en état
Pour mener à bien les opérations de remise en état, les techniciens de maintenance doivent disposer d’un ensemble d’outils et d’équipements adaptés. Ces outils leur permettent d’effectuer des diagnostics précis, de réaliser les réparations nécessaires et de valider le bon fonctionnement des équipements après intervention.
Multimètres et oscilloscopes pour le dépannage électrique
Les multimètres sont des outils indispensables pour tout technicien de maintenance. Ils permettent de mesurer les tensions, intensités et résistances dans les circuits électriques. Les modèles numériques offrent une grande précision et des fonctionnalités avancées comme la mesure de capacité ou de fréquence.
Les oscilloscopes sont particulièrement utiles pour analyser les signaux électroniques complexes. Ils permettent de visualiser la forme, l’amplitude et la fréquence des signaux, ce qui est essentiel pour diagnostiquer les problèmes sur les cartes électroniques ou les systèmes de contrôle.
Kits de soudure et stations de dessoudage
Pour la réparation des circuits électroniques, un kit de soudure de qualité est indispensable. Il doit comprendre un fer à souder à température réglable, différentes pannes adaptées aux composants à souder, ainsi que des accessoires comme une pompe à dessouder et de la tresse à dessouder.
Une station de dessoudage professionnelle facilite grandement le remplacement des composants sur les cartes électroniques denses. Elle permet de retirer proprement les composants défectueux sans endommager le circuit imprimé.
Logiciels de diagnostic et interfaces de programmation
Les logiciels de diagnostic spécifiques aux équipements industriels sont des outils précieux pour analyser en profondeur le fonctionnement des machines. Ils permettent d’accéder aux paramètres internes, de visualiser les données en temps réel et de configurer les systèmes de contrôle.
Les interfaces de programmation sont nécessaires pour mettre à jour le firmware des équipements ou modifier leur programmation. Elles peuvent prendre la forme de câbles spécifiques ou de modules de communication sans fil selon les technologies utilisées.
Équipements de protection individuelle (EPI) adaptés
La sécurité est primordiale lors des interventions de maintenance. Les techniciens doivent disposer d’EPI adaptés aux risques spécifiques de leur environnement de travail. Cela peut inclure des chaussures de sécurité, des lunettes de protection, des gants isolants pour les interventions électriques ou des masques de protection respiratoire pour les environnements poussiéreux.
La sécurité des techniciens est une priorité absolue. Aucune intervention ne doit être entreprise sans les équipements de protection appropriés.
En plus de ces équipements de base, certaines interventions peuvent nécessiter des outils spécialisés comme des caméras thermiques, des analyseurs de vibrations ou des endoscopes industriels. L’investissement dans ces technologies avancées permet souvent d’améliorer significativement l’efficacité des opérations de maintenance.
Procédures de test et de validation post-réparation
Après avoir effectué les réparations nécessaires, il est crucial de procéder à des tests rigoureux pour valider le bon fonctionnement de l’équipement remis en état. Ces procédures de test et de validation sont essentielles pour garantir la fiabilité et la sécurité de l’équipement avant sa remise en service.
La première étape consiste généralement en une série de tests fonctionnels. Il s’agit de vérifier que toutes les fonctions de l’équipement opèrent correctement, en simulant si possible les conditions réelles d’utilisation. Ces tests doivent couvrir l’ensemble des modes de fonctionnement de la machine, y compris les situations exceptionnelles ou les modes dégradés.
Des mesures précises doivent être effectuées pour s’assurer que les performances de l’équipement correspondent aux spécifications du constructeur. Cela peut inclure des mesures de vitesse, de précision, de consommation d’énergie ou de qualité de production selon le type d’équipement concerné.
La vérification des systèmes de sécurité est une étape cruciale. Tous les dispositifs de sécurité, qu’ils soient mécaniques, électriques ou électroniques, doivent être testés pour garantir leur bon fonctionnement. Cela inclut les arrêts d’urgence, les barrières immatérielles, les capteurs de présence ou les limiteurs de couple par exemple.
Dans certains cas, des tests d’endurance peuvent être nécessaires pour s’assurer de la fiabilité à long terme de la réparation. Il s’agit de faire fonctionner l’équipement pendant une période prolongée, parfois dans des conditions intensives, pour détecter d’éventuels problèmes qui n’apparaîtraient pas immédiatement.
Enfin, la documentation précise de tous les tests effectués et des résultats obtenus est essentielle. Ces rapports servent non seulement à valider la remise en service de l’équipement, mais aussi à alimenter l’historique de maintenance qui sera précieux pour les interventions futures.
Stratégies de maintenance préventive pour réduire les pannes
Si la remise en état rapide des équipements défaillants est cruciale, la mise en place de stratégies de maintenance préventive est tout aussi importante pour réduire la fréquence des pannes. Une approche proactive de la maintenance permet d’optimiser la disponibilité des équipements et de réduire les coûts liés aux arrêts imprévus.
La planification des interventions de maintenance préventive est au cœur de cette stratégie. Elle s’appuie sur les recommandations du constructeur, l’historique des pannes et l’analyse des données de fonctionnement des équipements. L’objectif est d’intervenir au moment optimal, ni trop tôt pour éviter des coûts inutiles, ni trop tard pour prévenir les défaillances.
L’inspection régulière des équipements est un élément clé de la maintenance préventive. Ces inspections permettent de détecter les signes précoces d’usure ou de dégradation avant qu’ils ne conduisent à une panne. Elles peuvent inclure des contrôles visuels, des mesures de vibrations, des analyses d’huile ou des thermographies infrarouges selon le type d’équipement.
Le remplacement programmé des pièces d’usure est une autre composante importante de la maintenance préventive. En remplaçant systématiquement certains composants avant qu’ils n’atteignent leur limite de durée de vie, on réduit considérablement le risque de pannes imprévues.
La lubrification régulière des équipements mécaniques est souvent négligée mais joue un rôle crucial dans la prévention des pannes. Un plan de lubrification précis, spécifiant les points à lubrifier, les types de lubrifiant à utiliser et les fréquences d’application, doit être établi et rigoureusement suivi.
L’analyse des données de fonctionnement des équipements, rendue
possible grâce aux technologies de l’Internet des Objets (IoT), ouvre la voie à la maintenance prédictive. Cette approche utilise des algorithmes d’intelligence artificielle pour détecter les anomalies et prédire les pannes avant qu’elles ne surviennent. Bien que son implémentation puisse être complexe, la maintenance prédictive offre un potentiel considérable pour optimiser la disponibilité des équipements et réduire les coûts de maintenance.
Formation et certification des techniciens de maintenance
La formation continue des techniciens de maintenance est essentielle pour maintenir un haut niveau d’expertise face à l’évolution rapide des technologies industrielles. Les programmes de formation doivent couvrir un large éventail de compétences, allant de la mécanique traditionnelle aux dernières avancées en électronique et en informatique industrielle.
Les formations techniques spécifiques aux équipements utilisés dans l’entreprise sont indispensables. Elles permettent aux techniciens de maîtriser les particularités de chaque machine et d’intervenir efficacement en cas de panne. Ces formations sont souvent dispensées par les fabricants d’équipements eux-mêmes ou par des organismes spécialisés.
La formation aux méthodes de diagnostic avancées est également cruciale. Les techniciens doivent être capables d’utiliser efficacement les outils modernes comme les analyseurs de vibrations, les caméras thermiques ou les logiciels de diagnostic. Des formations pratiques, mettant en situation les techniciens face à des pannes simulées, sont particulièrement efficaces pour développer ces compétences.
L’investissement dans la formation des techniciens est rentabilisé par une plus grande efficacité des interventions et une réduction des temps d’arrêt des équipements.
La certification des compétences des techniciens de maintenance est de plus en plus valorisée dans l’industrie. Des organismes comme l’Association Française de Normalisation (AFNOR) proposent des certifications reconnues qui attestent du niveau d’expertise des techniciens. Ces certifications peuvent couvrir des domaines spécifiques comme la maintenance prédictive, la fiabilité des équipements ou la sécurité des interventions.
Enfin, la formation aux compétences transversales ne doit pas être négligée. La capacité à communiquer efficacement, à travailler en équipe et à gérer le stress sont des atouts précieux pour les techniciens de maintenance qui interviennent souvent dans des situations d’urgence. Des formations au management peuvent également être bénéfiques pour les techniciens amenés à prendre des responsabilités d’encadrement.
En conclusion, la remise en état rapide des équipements défaillants est un défi complexe qui nécessite une combinaison de compétences techniques pointues, d’outils adaptés et de méthodologies efficaces. L’investissement dans la formation continue des techniciens et dans des technologies de pointe pour le diagnostic et la réparation est essentiel pour maintenir la compétitivité des installations industrielles. Couplée à une stratégie de maintenance préventive et prédictive, cette approche permet d’optimiser la disponibilité des équipements et de réduire significativement les coûts liés aux pannes imprévues.